Within this article, we shall delve into the fundamental aspects of stepper motors. Your understanding will encompass the operational principles, structural components, methods of control, applications, and classifications of stepper motors, along with their merits and drawbacks.
Dive into the Mechanics of a Stepper Motor: An In-Depth Analysis
Fundamental Building Blocks of Stepper Motors
Fundamentally, stepper motors are designed with two key components: a static component, known as the stator, and a dynamic part, alternately termed the rotor. The stator, a structure laden with teeth around which coils are systematically wired, serves as a stationary framework. The rotor, on the other hand, is either an enduring magnet or a variable reluctance iron core whose primary function is to move.
This section provides a detailed examination of the unique architectures of the rotor, which will be discussed later in this article. We will also present a graphical illustration to help readers visualize these complex structures. The illustration showcases the section of the motor, highlighting the rotor as a variable-reluctance iron core.
The Core Principle: How Does a Stepper Motor Work?
The functioning principle of a stepper motor hinges on the process of energizing the stator phases. This process generates a magnetic field due to the current flowing in the coil, which subsequently causes the rotor to align itself with this magnetic field. By strategically energizing different phases in a sequence, the rotor can be made to rotate by a certain degree to reach the intended final position.
To help readers better comprehend this complex mechanism, we provide a graphical illustration of the working principle of a stepper motor. The image sequence begins with the energization of coil A, resulting in the rotor aligning itself with the magnetic field produced by coil A. As coil B is energized, the rotor rotates in a clockwise direction by 60° to meet the new magnetic field. The same process is repeated when coil C is energized.
In the provided visualizations, the different colors of stator teeth signify the varied directions of the magnetic field produced by the stator winding. This distinction helps in understanding the transition of the magnetic field during the operation of a stepper motor.
Unraveling Stepper Motors: Types, Construction, and Performance Variations
Stepper motors display remarkable diversity in terms of their construction and operational dynamics. The intricate details of their construction significantly govern their performance metrics like resolution, speed, and torque. It’s also worth noting that these details can influence the control mechanisms of the stepper motor.
Like fingerprints, no two stepper motors have identical internal structures. The rotor and stator configurations vary, making each stepper motor exclusive in its operation and performance.
Rotor Configurations
Three primary types of rotors form the heart of a stepper motor:
- Permanent Magnet Rotor: As the name suggests, this rotor type involves a permanent magnet that undergoes alignment with the magnetic field generated by the stator circuit. This design promises substantial torque and a notable detent torque, enabling the motor to resist positional shifts even without any coil energization. The one hurdle with this arrangement is its comparably lower speed and resolution relative to other types. To help visualize this configuration, we’ve included an illustration of a permanent magnet stepper motor section.
In the quest to understand and harness the power of stepper motors, it’s essential to delve into their construction and how it influences their performance. By doing so, users can leverage the power of these versatile motors to suit their specific requirements.
Tips for optimal use:
- Always consider the application before choosing the motor type;
- Pay attention to the torque, speed, and resolution of the motor to determine its suitability for your specific application;
- Ensure that the control mechanism of the motor aligns with your operational necessities.
By following these tips, users can select the most suitable stepper motor, ensuring efficient and reliable operation. The deep understanding of the working principle and construction of stepper motors paves the way for maximizing their potential, leading to enhanced performance and productivity.
Delving Deeper: Variable Reluctance and Hybrid Rotors in Stepper Motors
Stepping motors’ functionality and efficiency are often determined by the rotor type in use. Essentially, rotors can fall into two other categories: Variable Reluctance Rotors and Hybrid Rotors, each with unique features that influence motor performance.
Variable Reluctance Rotor
A Variable Reluctance Rotor features an iron core. This distinct shape enables it to align accurately with the magnetic field, masterminded by the stator circuit. This rotor type boasts a higher speed and resolution capacity, making it an apt choice for applications demanding speed precision. However, where it wins in speed and resolution, it falls short in torque power and completely lacks in detent torque.
While the enhanced speed and resolution of Variable Reluctance Rotors offer advantages, keep in mind the trade-off with torque power when choosing motors for specific applications.
Hybrid Rotor
Treading the middle ground, Hybrid Rotors blend the best of both worlds. This rotor type combines the features of both Permanent Magnet and Variable Reluctance Rotors. Its structural detail includes two end caps with alternating teeth and an axial magnetization.
Thanks to this unique construction, Hybrid Rotors offer high resolution, speed, and torque power making them ideal for applications demanding an all-rounded performance. However, this high performance comes at a price – complex construction and consequently higher cost.
To shed light on the operational dynamics of Hybrid Rotors, a simplified model of the structure is provided. Note that actual motors possess a more complex structure with a substantial number of teeth, enabling them to achieve a minuscule step size down to 0.9°.
When selecting a stepper motor, it’s crucial to:
- Analyze the demands of your application;
- Understand the trade-offs between rotor types;
- Consider your budget while evaluating potential performance benefits.
By doing so, you can make an informed decision, selecting a stepper motor type that aligns optimally with your specific needs, budget, and application requirements.
The Stator: The Magnetic Field Conductor in Stepper Motors
In the grand symphony of a stepper motor’s operation, if the rotor is the star performer, the stator serves as the orchestra, setting the stage for the rotor’s movements. The stator plays a crucial role in creating the magnetic field that guides and controls the rotor’s alignment.
Just like the rotor, the stator contains its unique set of characteristics that significantly influence the motor’s overall performance. Comprehending these characteristics is crucial for understanding and optimizing the operation of stepper motors.
Key Characteristics of the Stator
- Number of Phases: The number of phases refers to the number of independent electrical circuits, or coils, found within the motor. Each phase can be energized independently, facilitating precise control over the motor’s rotation;
- Pole Pairs: The pole pairs indicate how many sets of teeth are occupied by each phase. By varying the number of pole pairs, you can zero in on the right balance between speed, torque, and control for your specific application;
- Wire Configuration: The stator’s winding or wire configuration also impacts its operation. The two most common configurations are unipolar and bipolar windings. Unipolar windings offer simplicity in control but deliver less torque, while bipolar windings provide high torque but require more complex control circuitry.
The most prevalent type of stator found in stepper motors have two phases. However, to meet varied operational demands, three-phase, and five-phase motors are also available, though these are less common.
For selecting the optimal stepper motor for your application, keep in mind to:
- Understand your application’s speed, torque, and control requirements;
- Evaluate the characteristics of the stator and rotor and how they match your requirements;
- Consider the complexity of control circuitry you are willing to handle.
With these factors taken into consideration, you can effectively choose a stepper motor that aligns with your operational demands, delivering outstanding performance and efficiency.
Controlling Stepper Motors: Key Components
The ability to precisely control the operations of a stepper motor, such as its speed, direction, and positional accuracy, sets it apart from other kinds of electrical motors. Three critical components drive this control mechanism, involving everything from current supply to signal generation. By understanding these components, users can effectively tap into the power of stepper motors to suit their specific needs.
Transistor Bridge
Serving as the gatekeeper, a transistor bridge controls the electrical connections of the motor’s coils, which ignites the magic in the stepper motor. A transistor operates much like a switch, controlling the flow of electrical current through a circuit. When activated or closed, it connects a coil to the electrical supply, which prompts the current to flow in the coil. Consequently, a magnetic field is created, essential for the rotor’s alignment. Each motor phase requires a separate transistor bridge.
Pre-Driver
Acting as the middleman between a microcontroller unit (MCU) and the transistor bridge, a pre-driver controls the transistors’ operations. It supplies the necessary voltage and current, as instructed by the MCU, to activate the transistors. This series of actions helps control the movement and positioning of the rotor.
Microcontroller Unit (MCU)
Regulating the entire show is the MCU. This programmable device emits specific signals for the pre-driver, commanding the desired motor behavior. Users can program the MCU to define the motor’s speed, direction, and position, yielding complete control over the stepper motor’s operation.
It’s important to:
- Understand the role of each component in a stepper motor control mechanism;
- Ensure the MCU is correctly programmed to achieve the desired motor behavior;
- Regularly maintain and check the components to ensure optimal operation.
Equipped with this understanding, users can harness the power of stepper motors, optimizing their operation for increased productivity and effectiveness. Careful consideration of these elements ensures appropriate control mechanisms, leading to robust motor performance and longevity.
Demystifying Stepper Motor Drivers: Types and Features
Stepper motor drivers are instrumental in the smooth functioning of a stepper motor. These devices govern the electrical supply to the motor, allowing it to operate correctly. Due to the diverse requirements presented by different applications, a variety of stepper motor drivers are available on the market, each with unique features and specifications.
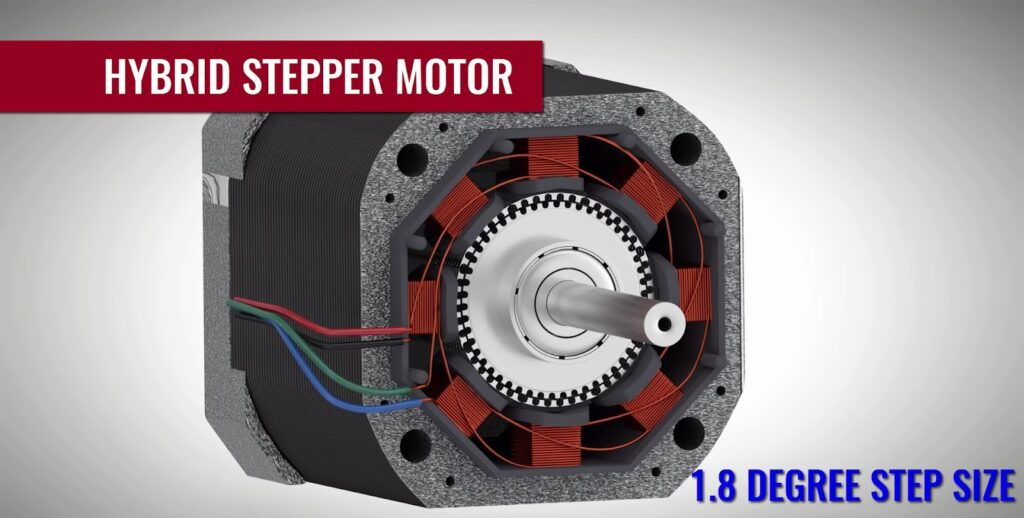
Input Interface Types
The input interface of a stepper motor driver is one of its most significant characteristics. Here are the three most common types:
- Step/Direction Interface: With this interface, each pulse sent to the Step pin prompts the driver to alter its output, causing the motor to perform a step. The direction of this step, either clockwise or counter-clockwise, is determined by the level on the Direction pin;
- Phase/Enable Interface: In this setup, the Phase and Enable prompts regulate each stator winding phase. While Phase determines the current direction, Enable triggers when the phase needs to be energized;
- PWM (Pulse Width Modulation) Interface: This interface directly controls the gate signals of the low-side and high-side Field-Effect Transistors (FETs), offering precise control over the motor’s speed and torque.
Control Mechanism
The control mechanism of a stepper motor driver takes into account two crucial factors: Voltage and Current.
- Voltage Control: These drivers regulate the voltage across the winding. In this case, the developed torque and the speed at which the steps are executed depend entirely on the motor and load characteristics;
- Current Control: More advanced than their voltage counterparts, these drivers control the current flowing through the active coil. By adjusting the current, the driver can control the torque produced, thereby managing the dynamic behavior of the entire system effectively.
As you select a stepper motor driver:
- Analyze the requirements of your application and the compatibility of the driver;
- Evaluate the type of control the driver offers and your requirement;
- Consider your budget constraint and the trade-off between cost and advanced features.
By carefully assessing these factors, you can select the most suitable stepper motor driver that aligns with your specific needs, optimizing the efficiency and performance of your stepper motor.
Understanding the Advantages and Disadvantages of Stepper Motors
Stepper motors are a fascinating piece of engineering that offers unique advantages and has its share of drawbacks. Delving into their workings and comparing them to other motor types sheds light on their distinct characteristics.
Advantages of Stepper Motors
- Position Sensing Simplicity: Unlike many other motor types that require external sensors for position detection, stepper motors inherently provide positional feedback through their step movements. This simplifies the control process and eliminates the need for additional sensors;
- Ease of Control: Stepper motor control is relatively straightforward compared to other motors. Although they require a driver, the control algorithms are less complex, reducing the overall control effort. This simplicity translates to easier integration into various systems;
- High Position Accuracy: With microstepping technology, stepper motors can achieve remarkable position accuracy, often up to approximately 0.007°. This precision is crucial for applications requiring exact positioning, such as CNC machines and 3D printers;
- Good Torque at Low Speeds: Stepper motors excel at delivering torque at low speeds, making them ideal for applications that demand precise movements and holding positions without the need for additional braking mechanisms;
- Long Lifespan: Stepper motors are known for their durability and longevity when properly maintained. Their robust construction and efficient operation contribute to a longer lifespan compared to some other motor types.
Disadvantages of Stepper Motors
- Potential Step Loss: Stepper motors can miss steps, especially when subjected to high load torque. This can lead to inaccurate positioning and affect the overall control performance of the motor system;
- Constant Current Draw: Stepper motors draw maximum current even when idle, which reduces their efficiency and can result in overheating issues over prolonged use;
- Noise at High Speeds: Stepper motors tend to produce considerable noise at higher speeds, which can be a concern in noise-sensitive environments or applications requiring quieter operation;
- Low Power Density: Compared to some other motor types, stepper motors have a lower power density, meaning they may not deliver as much power relative to their size and weight.
Unveiling the Versatile Applications of Stepper Motors
Stepper motors, known for their precise control and ability to maintain position, find diverse applications across various industries. Their unique properties make them indispensable in numerous cutting-edge technologies. Here are some expanded insights into the uses and applications of stepper motors:
1. Printers
- Printheads: Stepper motors control the precise movement of printheads in inkjet printers, ensuring accurate placement of ink droplets on paper;
- Paper Feed: Stepper motors power the mechanisms responsible for feeding paper through printers, maintaining consistent alignment and preventing jams;
- Scan Bar: In scanning devices, stepper motors facilitate the controlled movement of the scanning bar, resulting in high-resolution and clear image reproduction.
2. 3D Printers
- XY Table Drive: Stepper motors drive the XY table, governing the movement of the print head along the X and Y axes, crucial for intricate 3D printing designs;
- Media Drive: These motors are used to control the movement of the print medium, ensuring precise layering and accurate printing outcomes.
3. Robots
- Arms: Stepper motors enable robotic arms to move with precision, allowing them to perform delicate tasks with accuracy and repeatability;
- End Effectors: These motors power the gripping and manipulation mechanisms of robot end effectors, ensuring controlled and stable operation.
4. DSLR Cameras
- Aperture/Focus Regulation: Stepper motors play a vital role in adjusting aperture size and focusing mechanisms in DSLR cameras, contributing to sharp and well-exposed photographs.
5. Video Cameras
- Pan, Tilt, Zoom: Stepper motors drive the pan, tilt, and zoom functions in video cameras, facilitating smooth and controlled movement for capturing dynamic shots;
- Focus: Precise focus adjustments in video cameras are achieved through stepper motor control, ensuring sharp and clear footage.
6. Engraving Machines
- XY Table Motion: Stepper motors control the XY table movement in engraving machines, allowing for precise engraving patterns and designs on various materials.
7. ATM Machines
- Bill Movement: Stepper motors regulate the movement of bills inside ATM machines, ensuring accurate counting and dispensing;
- Tray Elevators: These motors are used in ATM tray elevators, enabling smooth and controlled movement of cash trays for efficient transactions.
Conclusion
In conclusion, stepper motors represent a versatile and widely used technology in various industries. Their precise control, robust construction, and suitability for numerous applications make them a valuable choice for many engineering and automation tasks. However, it’s essential to consider their limitations, such as potential overheating and complexity in high-speed operations, when selecting the appropriate motor for specific projects. Overall, stepper motors offer a balance of performance and flexibility that continues to drive innovation in the field of motion control.